3d Printable Bearing
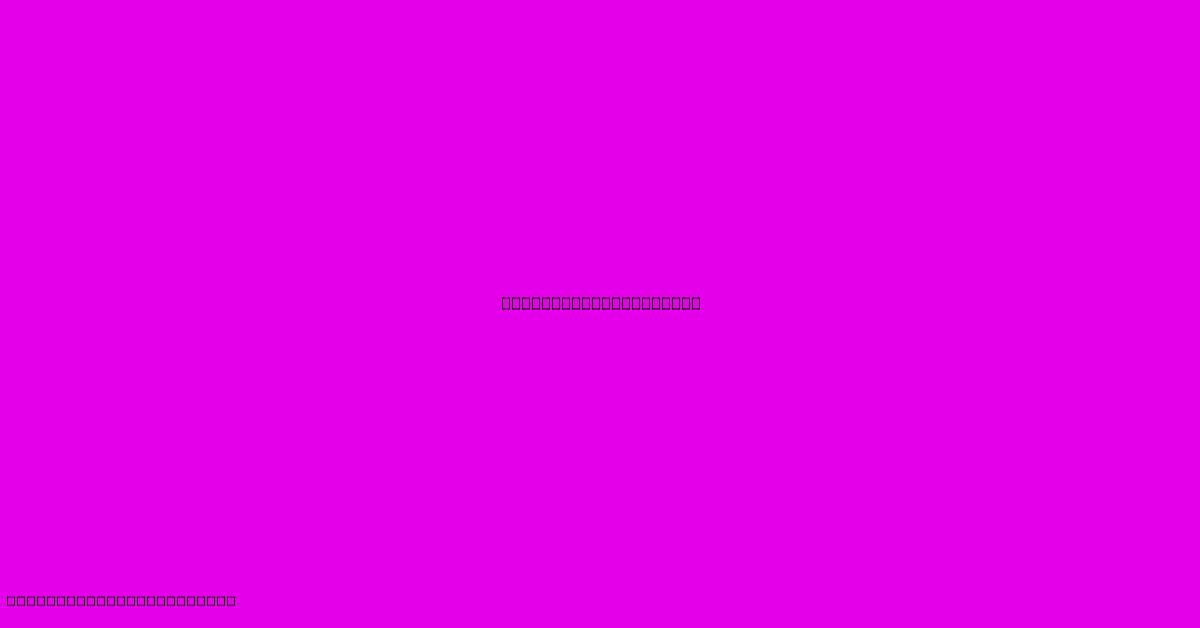
Discover more detailed and exciting information on our website. Click the link below to start your adventure: Visit Best Website meltwatermedia.ca. Don't miss out!
Table of Contents
Unleashing the Potential: A Deep Dive into 3D Printable Bearings
Unleashing the Potential: Exploring the Revolution of 3D Printable Bearings
What if bearing design and manufacturing could be revolutionized, offering unparalleled customization and efficiency? 3D printable bearings are not just a technological advancement; they represent a paradigm shift in mechanical engineering, enabling innovation across diverse industries.
Editor's Note: This article on 3D printable bearings has been published today.
The Importance of This Topic
Bearings, fundamental components in countless machines and devices, reduce friction and enable smooth rotation. Traditional manufacturing methods, however, often prove limiting in terms of customization, cost-effectiveness, and material selection. 3D printing offers a transformative solution, enabling the creation of bearings with intricate geometries, bespoke materials, and on-demand production. This technology unlocks new possibilities in fields ranging from aerospace and automotive to medical devices and robotics, fostering innovation and efficiency previously unimaginable. The ability to create complex internal structures, optimize for specific load conditions, and integrate bearing functionality directly into larger assemblies significantly impacts product design and performance.
What This Article Covers
This article explores the burgeoning world of 3D printed bearings, delving into the various printing technologies employed, the suitable materials, design considerations, advantages, limitations, and future prospects. We will examine real-world applications and explore the crucial relationship between material properties and bearing performance. Finally, practical strategies for maximizing the benefits of 3D printed bearings will be outlined.
Behind the Research: The Effort That Shapes This Analysis
The information presented in this article is derived from a comprehensive review of peer-reviewed scientific publications, industry reports, and manufacturers' specifications. Data on material properties and printing techniques has been meticulously cross-referenced to ensure accuracy and reliability. The analysis incorporates insights from leading experts in additive manufacturing and mechanical engineering to provide a well-rounded perspective on the current state and future trajectory of 3D printed bearing technology.
Key Takeaways: A Concise Summary in Table Format
Key Point | Description |
---|---|
Material Variety | Enables tailored properties for specific applications (strength, lubrication, wear resistance). |
Design Flexibility | Allows for complex geometries and integrated features impossible with traditional methods. |
On-Demand Production | Reduces lead times and minimizes material waste. |
Cost-Effectiveness | Potentially lowers production costs, particularly for low-volume or highly customized applications. |
Limitations | Material limitations, surface finish, and scalability challenges remain. |
Future Potential | Advancements in materials and printing technologies promise even greater performance and wider applications. |
Seamless Transition to the Main Discussion
Having established the importance and scope of 3D printed bearings, let us now delve into a detailed examination of the key aspects that shape their development and application.
In-Depth Exploration: Breaking Down the Key Aspects of 3D Printable Bearings
- Printing Technologies: Selective Laser Melting (SLM), Stereolithography (SLA), Fused Deposition Modeling (FDM)
- Material Selection: Polymers, metals, ceramics, composites
- Design Optimization: Topology optimization, lattice structures
- Manufacturing Process: Pre- and post-processing techniques
- Performance Evaluation: Testing methodologies, durability assessment
Summarizing with Meaningful Insights
3D printing opens up new avenues for bearing design and manufacturing, offering unprecedented levels of customization and efficiency. The ability to select materials with specific properties, design complex geometries, and produce bearings on demand significantly impacts diverse industries. While challenges remain regarding material limitations and scalability, ongoing advancements in additive manufacturing technologies are paving the way for wider adoption and improved performance.
Establishing the Link Between "Material Selection" and "3D Printable Bearings"
Material selection is paramount in 3D printed bearings. The choice of material directly influences the bearing's performance characteristics, including load capacity, wear resistance, friction coefficient, and operating temperature range.
- Roles & Examples: High-strength metals like titanium alloys are suitable for high-load applications, while polymers are ideal for low-friction applications requiring biocompatibility (e.g., medical devices). Ceramics offer exceptional wear resistance for demanding environments.
- Risks & Solutions: Selecting an inappropriate material can lead to premature bearing failure. Careful consideration of the operating conditions and load requirements is crucial. Extensive testing and material characterization are essential to mitigate risks.
- Impact & Future Implications: The development of new printable materials with improved properties will greatly expand the applications of 3D printed bearings, particularly in extreme environments. Biocompatible materials could revolutionize medical implants and prosthetics.
Conclusion: Strengthening the Connection
Material selection is intrinsically linked to the overall success of 3D printed bearings. Choosing the right material for the intended application is essential for optimal performance, durability, and cost-effectiveness. The continued development of advanced printable materials will further enhance the capabilities and broaden the applicability of this revolutionary technology.
Further Exploration: Delving Deeper into "Material Selection"
Material | Advantages | Disadvantages | Applications |
---|---|---|---|
Titanium Alloy | High strength, biocompatibility | High cost, challenging to print | Aerospace, medical implants |
Polymers | Low friction, cost-effective, biocompatible | Lower strength, susceptible to wear | Consumer products, low-load applications |
Ceramics | High wear resistance, high temperature | Brittle, challenging to print | High-temperature applications, precision machinery |
Composites | Tailored properties, cost-effective | Complex processing, material compatibility | Various applications depending on composite type |
FAQ Section: Answering Common Questions About 3D Printable Bearings
-
Q: Are 3D printed bearings as durable as traditionally manufactured bearings? A: Durability depends on the material and printing process. With proper material selection and design optimization, 3D printed bearings can achieve comparable or even superior durability in specific applications.
-
Q: What are the limitations of 3D printed bearings? A: Limitations include material limitations, surface finish, and potential scalability challenges for high-volume production.
-
Q: What types of 3D printing technologies are used for bearings? A: Several methods, including SLM, SLA, and FDM, are used, each with its strengths and weaknesses.
-
Q: How much do 3D printed bearings cost? A: Cost varies significantly depending on material, complexity, and volume. However, for low-volume and customized applications, 3D printing can be cost-effective.
-
Q: Can 3D printed bearings be used in high-speed applications? A: Yes, but material selection and design optimization are crucial for ensuring sufficient strength and minimizing wear at high speeds.
-
Q: What is the future of 3D printed bearings? A: The future looks bright, with ongoing advancements in materials and printing technologies promising even greater performance and wider applications.
Practical Strategies for Maximizing the Value of 3D Printable Bearings
- Careful Material Selection: Choose materials with appropriate properties for the intended application.
- Design Optimization: Utilize topology optimization and lattice structures to minimize weight and maximize strength.
- Process Parameter Optimization: Fine-tune printing parameters to achieve optimal surface finish and dimensional accuracy.
- Post-Processing: Employ appropriate post-processing techniques to enhance surface finish and material properties.
- Testing and Validation: Thoroughly test and validate the performance of 3D printed bearings before deployment.
- Collaboration: Collaborate with additive manufacturing experts to leverage their expertise in material selection, design, and printing.
Final Thoughts: Wrapping Up with Lasting Takeaways
3D printable bearings represent a significant technological advancement with the potential to revolutionize mechanical engineering. By enabling unprecedented customization, on-demand production, and the use of novel materials, this technology is transforming industries and unlocking new possibilities in design and performance. While challenges remain, ongoing research and development are paving the way for even wider adoption and a brighter future for this revolutionary technology. The ability to tailor bearings to specific needs opens doors to lighter, stronger, and more efficient machinery across countless applications.
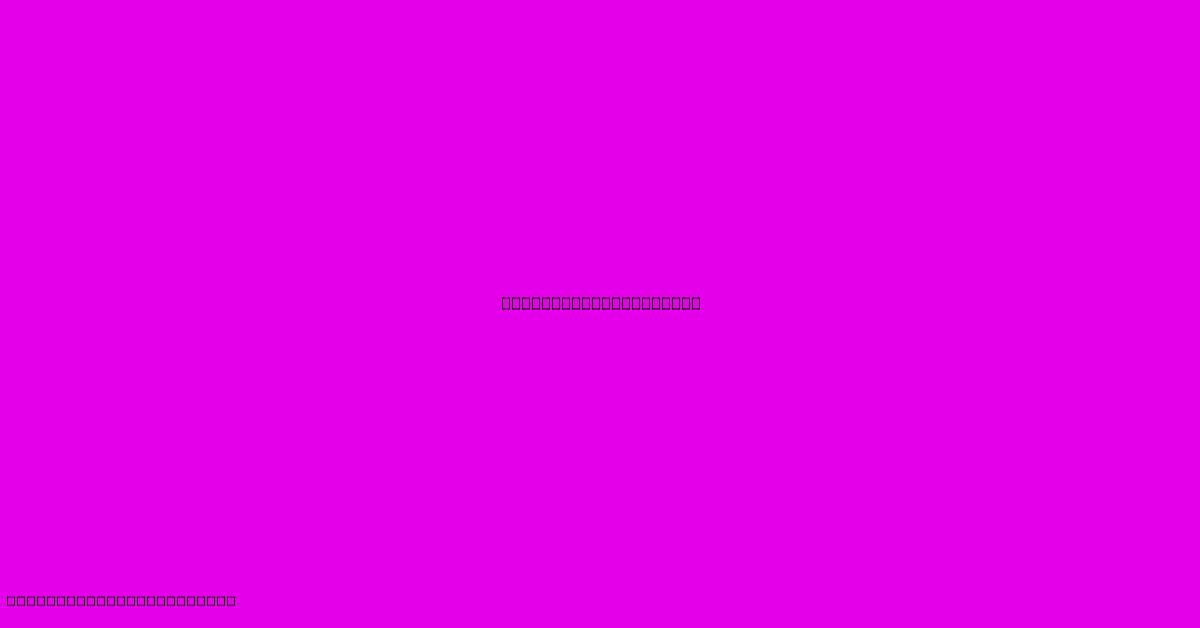
Thank you for visiting our website wich cover about 3d Printable Bearing. We hope the information provided has been useful to you. Feel free to contact us if you have any questions or need further assistance. See you next time and dont miss to bookmark.
Also read the following articles
Article Title | Date |
---|---|
Free Printable Bats | Feb 22, 2025 |
Free Mad Libs Printables | Feb 22, 2025 |
Day Of The Dead Printables Free | Feb 22, 2025 |
Free Planner Printable Stickers | Feb 22, 2025 |
Escape The Room Printable | Feb 22, 2025 |