Laser Printable Plastic
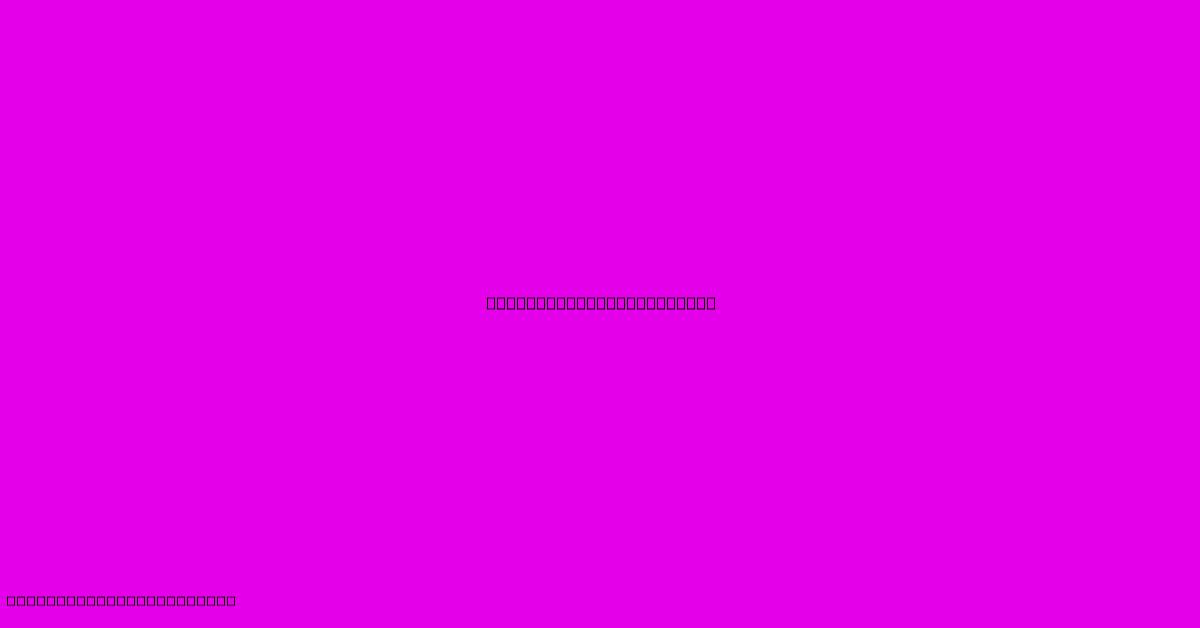
Discover more detailed and exciting information on our website. Click the link below to start your adventure: Visit Best Website meltwatermedia.ca. Don't miss out!
Table of Contents
Unlock the Potential: A Deep Dive into Laser Printable Plastics
What if you could seamlessly blend the durability of plastic with the precision of laser printing? Laser printable plastics are revolutionizing industries, offering a powerful combination of design flexibility and robust material properties.
Editor Note: Laser Printable Plastics has been published today.
The Importance of This Topic
Laser printable plastics represent a significant advancement in manufacturing and design. They bridge the gap between digital design and physical production, enabling rapid prototyping, personalized products, and highly customized solutions across various sectors. From automotive and aerospace to medical devices and consumer goods, the ability to directly print onto durable plastic substrates unlocks unprecedented levels of efficiency and creative freedom. This material's impact extends beyond specialized industries; its potential for personalized items and on-demand production is reshaping how we approach manufacturing and consumption. Understanding its properties, applications, and limitations is crucial for businesses and designers alike seeking innovative and cost-effective solutions.
What This Article Covers
This article provides a comprehensive overview of laser printable plastics, exploring their properties, applications, the printing process, key considerations for successful printing, and future trends. We will delve into the advantages and disadvantages, highlighting best practices for maximizing the value of this versatile material.
Behind the Research: The Effort That Shapes This Analysis
This analysis is based on extensive research encompassing peer-reviewed scientific publications, industry reports, manufacturer specifications, and case studies demonstrating real-world applications of laser printable plastics. Data from various sources has been meticulously analyzed to provide a balanced and informative perspective on this rapidly evolving technology.
Key Takeaways: A Concise Summary in Table Format
Key Feature | Description |
---|---|
Material Types | PETG, ABS, Polycarbonate, and specialized blends |
Printing Process | Laser toner fusion or direct laser etching/engraving |
Advantages | High durability, design flexibility, rapid prototyping, cost-effectiveness |
Disadvantages | Material limitations, specialized equipment, potential for warping |
Key Applications | Prototyping, signage, personalized products, medical devices, automotive parts |
Seamless Transition to the Main Discussion
From its origins in niche applications to its current widespread adoption, laser printable plastic has consistently demonstrated its potential to transform industries. Let's explore the key aspects shaping its rising prominence.
In-Depth Exploration: Breaking Down the Key Aspects of Laser Printable Plastics
- Material Types: PETG, ABS, Polycarbonate
- Printing Process: Toner fusion, laser etching
- Applications: Prototyping, product customization
- Advantages: Durability, versatility
- Disadvantages: Cost, specialized equipment
Summarizing with Meaningful Insights
Laser printable plastics offer a compelling blend of material strength and digital design precision. This synergy facilitates rapid prototyping, customized production runs, and the creation of highly specialized parts. The inherent durability of these plastics, coupled with the precision of laser printing, makes them a valuable asset across various industries, paving the way for innovations in product design and manufacturing. Their use in personalized gifts, bespoke medical devices, and intricate automotive components exemplifies their versatility and potential for future growth.
Establishing the Link Between "Material Selection" and "Laser Printable Plastics"
Roles & Examples โ How does "Material Selection" influence "Laser Printable Plastics"? The success of laser printing on plastics hinges on selecting the appropriate material. ABS, for instance, offers high impact resistance, making it suitable for durable products. PETG provides a good balance of strength and flexibility, while polycarbonate boasts exceptional clarity and impact strength, ideal for specialized applications like medical devices or clear signage. Incorrect material selection can lead to subpar results, such as warping, cracking, or poor adhesion of the printed image.
Risks & Solutions โ What are the potential challenges, and how can they be mitigated? Warpage is a common risk, especially with thicker plastic sheets. This can be minimized by using a pre-heated bed, controlling the laser power settings, and selecting materials with lower thermal expansion coefficients. Adhesion issues can be addressed by using specialized primers or surface treatments. Poor print quality might result from incorrect laser settings or low-quality toner.
Impact & Future Implications โ What are the broader consequences and long-term effects? The increasing accessibility and affordability of laser printable plastics are driving innovation in various sectors. The ability to create highly customized and personalized products on demand will reshape manufacturing processes and consumer expectations. Future developments might include biodegradable laser printable plastics and materials with enhanced properties for specific applications.
Conclusion: Strengthening the Connection
Laser printable plastics are rapidly transforming the landscape of manufacturing and design. Careful consideration of material selection, laser parameters, and potential challenges is crucial for achieving optimal results. The potential for further innovation in material properties and printing technologies promises even greater flexibility and efficiency in the years to come.
Further Exploration: Delving Deeper into "Printing Process"
The printing process involves either laser toner fusion or direct laser etching/engraving. In toner fusion, the laser heats the toner, causing it to fuse with the plastic surface. The process is similar to standard laser printing but requires specialized plastics and printers capable of handling the higher temperatures. Direct laser engraving, on the other hand, uses the laser to ablate or remove material from the surface, creating a permanent mark. This technique is particularly useful for detailed designs or for creating textured surfaces.
Method | Description | Advantages | Disadvantages |
---|---|---|---|
Toner Fusion | Laser heats toner to fuse with plastic surface | Relatively simple, widely available technology | Requires compatible plastics, toner quality matters |
Laser Engraving | Laser ablates material to create design | High precision, durable results | Can be slower, requires more powerful lasers |
FAQ Section: Answering Common Questions About Laser Printable Plastics
-
Q: What types of lasers are used for printing on plastics? A: CO2 lasers and fiber lasers are commonly used, depending on the material and printing method.
-
Q: Are all plastics laser printable? A: No, only specific types of plastics are compatible with laser printing due to their melting points and absorption characteristics.
-
Q: How durable are laser-printed plastics? A: Durability depends on the plastic type and the printing process. Properly printed parts can be very durable, resisting scratches and chemicals.
-
Q: Is laser printing on plastic expensive? A: The cost depends on the equipment, materials, and complexity of the design. It can be cost-effective for small-batch production and prototyping.
-
Q: What safety precautions should be taken when laser printing on plastics? A: Always wear appropriate safety glasses and ensure adequate ventilation to avoid exposure to fumes and laser radiation.
-
Q: Can I laser print on plastic at home? A: While small-scale laser engravers are available for home use, laser printing with toner typically requires more specialized equipment.
Practical Strategies for Maximizing the Value of Laser Printable Plastics
- Choose the right material: Select a plastic based on the application's required properties.
- Optimize laser settings: Adjust power, speed, and passes to achieve optimal results.
- Use a pre-heated bed: Prevent warping by printing on a heated surface.
- Apply primer (if necessary): Improve adhesion for better print quality.
- Design for manufacturability: Consider the limitations of the printing process when designing your part.
- Test and iterate: Conduct test prints to fine-tune settings and avoid costly errors.
- Utilize design software: Employ specialized CAD software for optimal results.
- Properly clean and maintain equipment: Ensuring the equipment is clean will extend its lifespan.
Final Thoughts: Wrapping Up with Lasting Takeaways
Laser printable plastics are poised to revolutionize design and manufacturing. Their unique combination of strength, versatility, and digital design integration opens doors to unprecedented levels of innovation across diverse industries. By understanding the key considerations, implementing best practices, and embracing ongoing advancements, businesses and designers can unlock the full potential of this transformative technology, shaping a future where creative visions are rapidly translated into robust, functional realities.
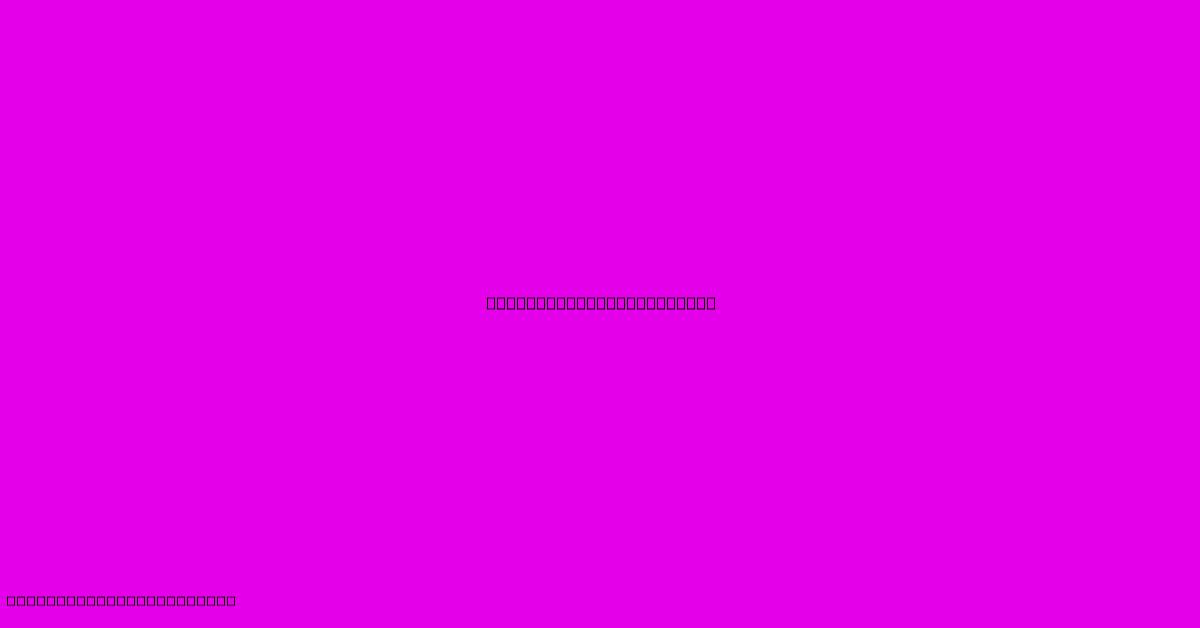
Thank you for visiting our website wich cover about Laser Printable Plastic. We hope the information provided has been useful to you. Feel free to contact us if you have any questions or need further assistance. See you next time and dont miss to bookmark.
Also read the following articles
Article Title | Date |
---|---|
I Love You Printable Card | Feb 23, 2025 |
Iowa Womens Basketball Schedule 23 24 Printable Free Download | Feb 23, 2025 |
Free Printable Fall Bingo | Feb 23, 2025 |
Free Printable Ninja Turtle Invitation Templates | Feb 23, 2025 |
Free Printable Lemonade Sign Printable | Feb 23, 2025 |